Survival no longer belongs to the biggest — it belongs to the fastest, smartest, and most adaptable. And the secret behind the industry’s most agile players? Digitally engineered workflows.
We’re not just talking about automation or digital tools. We’re talking about redefining how products are imagined, designed, built, and delivered — from concept to customer. This isn’t evolution. It’s reinvention.
Let’s unpack why digitally engineered workflows are not just a trend — they’re the backbone of next-generation manufacturing.
⚙️ First, What Exactly Are Digitally Engineered Workflows?
Digitally engineered workflows unify design, production, and operational data through connected systems, cloud collaboration, real-time feedback loops, and intelligent automation.
It’s about engineering smarter — virtually first, physically second. Imagine simulating an entire factory process, running thousands of iterations, identifying faults, and optimizing everything — before you even switch on a machine.
See Why Industry Leaders Are All-In on Production Management Tech — Read the 2025 Insider Breakdown and Learn How to Stay Competitive, Agile, and Profitable in the Next Era of Manufacturing.
This is precision at scale, powered by tech like:
Digital twins
AI-driven analytics
Cloud-based PLM
Smart sensors and IoT
Simulation and predictive modeling
🔍 Why This Shift Is Inevitable — and Urgent
The old ways are breaking under pressure. Disruption is no longer rare — it’s constant. And in that reality, manual, reactive, and siloed processes simply can’t compete.
Here’s why digitally engineered workflows are now mission-critical:
✅ 1. Collapse Time-to-Market
Markets are moving faster than ever. Digitally engineered workflows cut months off development cycles. What used to take 12 months can now take 12 weeks — thanks to virtual prototyping, automated testing, and real-time feedback.
✅ 2. Build Resilient, Responsive Operations
Digitally connected factories don’t just automate — they adapt. When a supply chain disruption hits, smart systems dynamically replan workflows, source alternatives, and adjust outputs on the fly.
✅ 3. Customize Without Compromise
Mass production is giving way to mass personalization. Digital engineering makes it possible to tweak designs, tooling, and production paths dynamically — enabling one-off or short-run variations without ballooning costs.
✅ 4. Supercharge Efficiency & Sustainability
Why wait to find out what went wrong? Predict it. Prevent it. Digitally engineered workflows allow for:
40% reduction in scrap
30% improvement in energy efficiency
50% faster defect detection
All while meeting strict ESG standards and improving margins.
✅ 5. Future-Proof Your Workforce
Give engineers AI copilots. Give technicians augmented reality instructions. Give managers real-time dashboards. When you digitize the workflow, you elevate the people behind it.
🧠 Technology in Action: What’s Powering the Revolution?
Tech Role
Digital Twins Model entire systems virtually for continuous optimization
AI & ML Predict failures, recommend improvements, optimize quality
Cloud Platforms Enable global collaboration, live data sync, remote access
IoT & Smart Sensors Generate data-rich environments with real-time insights
Simulation Software Test thousands of variables before physical execution
Ready to Revolutionize Your Shop Floor? Let’s Develop Custom Manufacturing Software That Fits Your Workflow, Eliminates Bottlenecks, and Powers Your Next Stage of Growth — Book a Free Strategy Session Today.
🚀 Real Companies. Real Results.
BMW uses digital twins to simulate its entire assembly lines, improving flexibility and cutting setup times by 30%.
Unilever integrated AI into its manufacturing, reducing energy use by up to 20%.
Boeing employs digitally engineered workflows to coordinate design-to-delivery for over 500,000 parts per aircraft — in near real-time.
These aren’t just digital transformations — they’re competitive advantages.
🧭 The Bottom Line: It’s Not “If” — It’s “When”
The question is no longer whether to digitize. The question is: how fast can you transition?
In the era of Industry 4.0 — and now Industry 5.0 — companies that fail to build digitally engineered workflows will lose their edge to those who do. Period.
✅ Faster innovation
✅ Lower cost per unit
✅ Greater quality control
✅ Higher resilience
✅ Sharper customer focus
This is the blueprint of the factory of the future. And the door is open — right now.
💬 Final Word: Are You Ready to Lead or Follow?
Digitally engineered workflows aren’t a project. They’re a mindset. A business model. A foundation for what comes next.
Leaders engineer their workflows. Laggards inherit their problems. Which one are you planning to be?
Let’s turn your production line into a competitive weapon — powered by digital precision and future-ready agility.
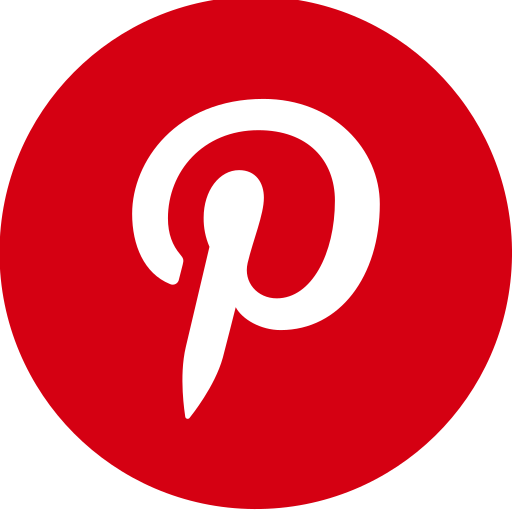