In Malaysia’s rapidly evolving electronics manufacturing sector, HAZOP (Hazard and Operability) reviews have become more than just a regulatory requirement—they’re a crucial safeguard for operational excellence and safety.
The importance of HAZOP reviews for electronics manufacturers in Malaysia stems from the increasing complexity of manufacturing processes and stringent safety regulations. These systematic assessments help identify potential hazards, evaluate operational risks, and establish robust safety protocols before they become critical issues.
In this guide, we’ll explore why HAZOP reviews are indispensable for electronics manufacturers in Malaysia.
Understanding HAZOP Studies in Electronics Manufacturing
A HAZOP study is a structured and systematic approach to identifying potential hazards and operational problems in manufacturing processes. In the electronics manufacturing sector, these studies are particularly crucial due to the complex nature of operations and the potential risks involved.
Core Components of HAZOP Assessment
The foundation of a successful HAZOP study in electronics manufacturing lies in its systematic approach to risk identification and assessment. This operability study begins with a detailed examination of the manufacturing process, breaking it down into manageable nodes or sections.
A comprehensive HAZOP assessment involves several key elements that work together to ensure thorough evaluation:
- Team Formation: Assembling a diverse group of experts including process engineers, operators, and safety specialists
- Process Documentation: Gathering detailed process flow diagrams, operating procedures, and technical specifications
- Node Identification: Breaking down the manufacturing process into distinct sections for detailed analysis
- Parameter Analysis: Examining process variables like temperature, pressure, and flow rates
- Deviation Assessment: Evaluating potential deviations from normal operating conditions
In the process industry of electronics manufacturing, HAZOP studies focus particularly on critical areas such as:
- Chemical storage and handling systems
- Waste treatment facilities
- Production line safety mechanisms
- Quality control checkpoints
- Emergency response systems
The systematic evaluation ensures that each aspect of the manufacturing process undergoes thorough scrutiny, identifying potential hazards that could affect both safety and operational efficiency.
Critical Safety Challenges in Malaysian Electronics Manufacturing
Malaysia’s process safety landscape in electronics manufacturing faces unique challenges that demand careful attention and systematic risk management approaches. The industry’s rapid growth has brought increased complexity to manufacturing processes, making safety considerations more critical than ever.
Common Process Safety Risks
The electronics manufacturing sector encounters various potential hazards throughout its industrial process chain. Chemical exposure during PCB manufacturing, high-voltage electrical risks, and thermal management issues pose significant threats to worker safety and operational efficiency.
Equipment malfunctions and process deviations can lead to serious operational issues if not properly monitored and controlled. These challenges are particularly evident in high-volume production environments where maintaining consistent safety standards becomes increasingly complex.
The integration of automated systems, while improving efficiency, introduces new safety considerations that manufacturers must address. From robotic assembly lines to chemical handling systems, each component adds another layer of complexity to the safety equation.
Temperature control and ventilation systems play crucial roles in preventing workplace accidents and maintaining optimal working conditions. Proper management of these systems is essential for preventing both immediate hazards and long-term health risks to workers.
Regulatory Framework and Compliance Requirements
Malaysian Safety Standards
In Malaysia, electronics manufacturers must adhere to stringent regulatory compliance frameworks that govern industrial safety and operational protocols. The Department of Occupational Safety and Health (DOSH) plays a pivotal role in establishing and enforcing these safety standards across the manufacturing sector.
The regulatory landscape encompasses both local and international standards, ensuring comprehensive coverage of safety protocols. Malaysian electronics manufacturers must comply with MS 1722:2011, the national safety standard that aligns with international best practices. This standard provides a structured approach to occupational safety and health management systems.
The National Institute of Standard and Industrial Research Malaysia (SIRIM) works alongside DOSH to develop and maintain these standards. They regularly update requirements to match evolving industry needs and technological advancements. These standards cover various aspects of manufacturing operations, including:
- Equipment safety protocols
- Chemical handling procedures
- Emergency response systems
- Risk assessment methodologies
- Worker safety training requirements
Beyond national regulations, Malaysian manufacturers must also align with international standard requirements, particularly when exporting to global markets. This includes compliance with ISO 45001 for occupational health and safety management systems.
The integration of these standards helps create a robust safety framework that:
- Minimizes operational risks
- Enhances worker protection
- Ensures process reliability
- Maintains quality control
- Supports sustainable operations
Regular audits and inspections by regulatory bodies ensure continued compliance and identify areas for improvement. This proactive approach helps manufacturers maintain high safety standards while meeting both local and international requirements.
Implementing Effective HAZOP Reviews
A successful HAZOP study requires meticulous planning and execution to identify potential hazards and operational issues effectively. The systematic approach ensures comprehensive risk assessment and mitigation strategies that protect both personnel and assets.
Team Formation and Roles
The foundation of any HAZOP review lies in assembling a diverse team of experts with complementary skills and knowledge. The team typically includes:
- Process Engineers
- Operations Personnel
- Safety Specialists
- Maintenance Representatives
- Quality Control Experts
- Environmental Specialists
Each member brings unique insights and perspectives, contributing to a thorough analysis of potential hazards. The HAZOP team must work cohesively, with clearly defined roles and responsibilities to ensure systematic evaluation of all process parameters.
Effective communication within the team is crucial for success. Regular meetings and structured discussions help identify potential issues that might be overlooked by individual team members. The team leader plays a vital role in:
- Facilitating open dialogue
- Managing time effectively
- Ensuring all viewpoints are considered
- Documenting findings accurately
- Maintaining focus on objectives
The HAZOP team should also include subject matter experts who can provide detailed technical insights when needed. Their expertise helps in:
- Understanding complex process interactions
- Identifying potential failure modes
- Evaluating consequences of deviations
- Proposing practical solutions
- Validating proposed safeguards
To maintain effectiveness, the team should establish clear communication channels and reporting structures. Regular updates and progress reports help track the review’s advancement and ensure all identified issues are properly addressed.
The success of a HAZOP review largely depends on the team’s ability to:
- Maintain objectivity throughout the process
- Follow systematic methodology
- Document findings comprehensively
- Propose practical recommendations
- Monitor implementation progress
Modern Approaches to Risk Assessment
Integration of Technology
The landscape of risk assessment in electronics manufacturing has evolved significantly with the integration of advanced technology. Modern approaches have transformed traditional risk assessment schemes into more sophisticated, data-driven processes that enhance accuracy and efficiency.
Digital tools and software platforms now enable manufacturers to conduct comprehensive risk assessments with greater precision. These technologies facilitate real-time monitoring, data collection, and analysis, moving beyond the limitations of manual risk management methods.
Advanced analytics and artificial intelligence play a crucial role in identifying potential hazards that might be overlooked in traditional risk assessment approaches. These tools can process vast amounts of data to detect patterns and predict potential risks before they materialize.
The risk-based approach has been revolutionized through:
- Real-time monitoring systems
- Automated data collection
- Predictive analytics
- Digital documentation management
- Integrated reporting systems
Modern technology also enables better collaboration among team members during risk assessment processes. Cloud-based platforms allow multiple stakeholders to contribute simultaneously, ensuring a more thorough evaluation of potential hazards.
The integration of IoT sensors and smart devices provides continuous monitoring capabilities, offering a more dynamic approach to risk management. This real-time data collection helps identify emerging risks and allows for immediate corrective actions.
Furthermore, digital dashboards and visualization tools make it easier to communicate risk assessment findings to stakeholders. These tools present complex data in an easily digestible format, facilitating better decision-making and risk mitigation strategies.
Machine learning algorithms can analyze historical data to predict future risks, moving beyond reactive approaches to proactive risk management. This predictive capability helps manufacturers address potential issues before they impact operations.
Also read: Managing Workplace Accidents and Injuries with OSHA’s Risk Control Methods
Documentation and Follow-up Procedures
Maintaining Assessment Records
Proper documentation forms the cornerstone of effective HAZOP reviews in Malaysia’s electronics manufacturing sector. Every assessment detail, from initial findings to implemented solutions, must be meticulously recorded to ensure transparency and accountability.
Creating comprehensive records involves documenting team compositions, meeting minutes, identified hazards, and recommended control measures. These records serve as valuable references for future assessments and demonstrate compliance with regulatory requirements.
A robust follow-up action system helps track the implementation of recommended safety measures. This includes assigning responsibilities, setting deadlines, and monitoring progress through regular status updates. Electronics manufacturers must establish clear protocols for reviewing and updating these records periodically.
Documentation practices should support continuous improvement initiatives by:
- Maintaining digital and physical copies of all assessment reports
- Recording dates of implementations and modifications
- Tracking the effectiveness of implemented solutions
- Documenting lessons learned and best practices
- Creating accessible databases for quick reference
Regular review of these records helps identify patterns, recurring issues, and areas requiring additional attention. This systematic approach ensures that safety measures evolve with changing manufacturing processes and technologies.
Best Practices for Sustainable Safety Management
Implementing sustainable safety management requires a systematic approach that combines technical expertise with continuous improvement strategies. Organizations must focus on developing robust safety protocols while fostering a culture of safety awareness among their workforce.
Industry-Specific Applications
The electronics manufacturing sector in Malaysia demands specialized best practice implementations that align with unique operational challenges. Technical skill development plays a crucial role in maintaining safety standards across different production phases.
A comprehensive safety management system relies on the collaborative efforts of multidisciplinary teams, bringing together expertise from various departments. This integrated approach ensures that safety protocols are both practical and effective.
To improve safety standards sustainably, manufacturers should:
- Implement regular safety audits and assessments
- Provide continuous training and skill development programs
- Establish clear communication channels for safety concerns
- Develop and maintain detailed documentation systems
- Create response protocols for emergency situations
Success in sustainable safety management comes from combining technical expertise with practical implementation strategies. Regular reviews and updates of safety protocols ensure they remain relevant and effective over time.
Organizations should also focus on:
- Building a strong safety culture through leadership commitment
- Encouraging employee participation in safety initiatives
- Investing in modern safety monitoring technologies
- Maintaining transparent reporting systems
- Conducting regular emergency response drills
Also read: Role of Health and Safety Audits in Achieving Zero Accident Construction Sites
Conclusion
As Malaysia’s electronics manufacturing sector continues to evolve, implementing HAZOP reviews isn’t just about meeting regulatory requirements—it’s about fostering a culture of safety and operational excellence. Through systematic hazard identification, comprehensive risk assessments, and robust safety protocols, manufacturers can protect their assets, personnel, and bottom line. The success of HAZOP reviews relies heavily on the collaborative efforts of multidisciplinary teams, proper documentation, and continuous improvement. By following industry best practices and maintaining regular reviews, electronics manufacturers can stay ahead of potential hazards while optimizing their processes for maximum efficiency and safety. Remember, in the realm of industrial safety, proactive measures always prove more valuable than reactive solutions. Your commitment to safety through HAZOP implementation will not only ensure regulatory compliance but also position your organization as a leader in responsible manufacturing.
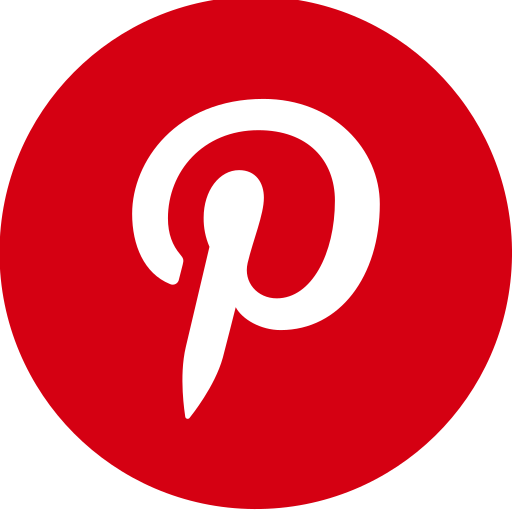