Cities thrive by building upward and outward—but construction sites remain some of the most dangerous workplaces. In high-growth areas like Los Angeles, the pressure of tight timelines and rising costs often leads to safety planning taking a back seat. When that happens, the consequences can be staggering.
According to national safety data, construction accidents cost employers over $13 billion annually in medical expenses, lost productivity, and legal claims. Nearly 1 in 5 workplace fatalities in the U.S. occurs on a construction site. And the effects reach far beyond the immediate injury—they disrupt entire projects, drain budgets, and damage reputations.
That’s why many victims quickly turn to legal professionals, such as a Los Angeles construction accident lawyer, to protect their rights and uncover what went wrong. ? Keep reading.
1. Project Timelines Break Down Without Safety as a Priority
When safety protocols aren’t embedded in the design or timeline, even minor issues can trigger major disruptions. A scaffold collapse, a short circuit, or improper ventilation due to rushed MEP layout can bring work to a standstill.
Industry data shows poor planning alone can stretch a project’s timeline by 15% or more. Delays compound when subcontractors are left waiting or when emergency fixes interrupt the flow. Trying to recover with overtime or weekend work may patch the surface—but the real cost lies in inefficiency, poor coordination, and client dissatisfaction.
2. Injury Claims Escalate Quickly and Expensively
Cutting corners on safety—especially in the early planning of Structural Design—leaves openings for serious incidents. When accidents happen due to overlooked hazards, legal claims aren’t far behind. Workers, visitors, or nearby residents may file lawsuits against contractors, property owners, or developers.
If documentation is lacking or safety logs are inconsistent, defending your firm becomes difficult. Settlements for major injuries can reach millions. A construction accident lawyer will look for red flags—like missing safety reviews during MEP system design, outdated equipment specs, or missed toolbox talks—to demonstrate negligence.
Beyond money, the reputational hit can be even more damaging.
3. Insurance Costs Skyrocket After a Single Incident
One major accident, especially one tied to flawed Structural or MEP design, can make your company a red flag to insurers. Premiums rise—sometimes by 25% or more—and coverage becomes limited or harder to renew.
Even if no lawsuit is filed, insurance providers may raise deductibles or reduce protection. These costs either get passed on to clients or erode profit margins. What’s worse, safety planning that should’ve been part of the initial design now becomes a reactive scramble to stay insurable.
4. Unsafe Sites Damage Worker Trust and Client Loyalty
Crews notice when a site lacks proper safety. Whether it’s exposed wiring, poor ventilation, or unclear site access, unsafe working conditions erode trust. Workers leave, and word spreads. One industry study found 70% of construction professionals would walk off a job due to safety concerns.
High turnover, bad reviews, and even public reporting can chase away not just labor but future clients. In contrast, contractors who prioritize safety in both their Structural and MEP design stages build long-term relationships and repeat business.
5. Code Violations Trigger Fines and Costly Work Stoppages
Code violations aren’t just technical—they’re expensive. Inspectors cite missing safety railings, mislabeled systems, or incomplete MEP documentation. Fines can hit $15,000 per violation, and repeat offenses can shut down an entire site.
Often, these issues stem from poor design coordination or skipped safety checks during the structural or mechanical layout phase. Fixing things after inspection creates pressure, stress, and rushed decisions—making the site even riskier in the long run.
Conclusion
Poor safety planning hurts more than just people—it hits your timeline, your wallet, and your reputation. It builds on itself until one incident sets everything off track.
If safety planning was skipped and someone was hurt, consider talking to a legal expert early. It helps uncover the cause, hold responsible parties accountable, and protect your future on or off the job.
For projects that prioritize safety from the blueprint to the final build, Structural and MEP Design must lead with risk prevention in mind. That’s where S3DA Design Firm stands out—bringing proactive, safety-integrated solutions to every phase of construction.
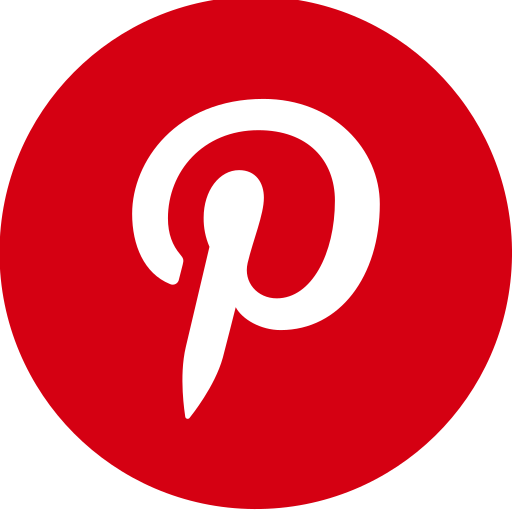