ISO 9001 certification isn’t just some fancy badge to stick on your marketing materials. It’s a comprehensive commitment to quality that drives efficiency, consistency, and growth. Whether you’re running a small-scale operation or a sprawling industrial facility, the decision to get ISO 9001 certified can profoundly impact your business—and trust us, it’s not as intimidating as it sounds. If you’re here wondering what it all means and if it’s really worth the effort, stick with us. Let’s break it down.
So, What Exactly is ISO 9001?
ISO 9001 is the most recognized standard for quality management systems (QMS) around the globe. Developed by the International Organization for Standardization (ISO), it lays out the criteria for establishing a robust system that ensures products and services consistently meet customer requirements and that quality is continuously improved.
Now, before you zone out thinking this is just another set of complicated regulations, let me tell you: ISO 9001 is all about creating smoother, more efficient systems that work for you, not against you.
Why Should Manufacturing and Industrial Companies Care?
You might be thinking, “I’ve been running my business just fine without it,” and hey, that might be true. But here’s the thing: ISO 9001 isn’t just about ticking boxes. It’s a strategic move that can give your company a serious edge.
Imagine you’re on a factory floor, machines humming, parts getting assembled. Everything seems fine, right? But what if a small defect slips through the cracks and ends up costing you big time—whether in terms of customer dissatisfaction, wasted resources, or even a recall? ISO 9001 helps you set up processes to minimize those risks, ensuring everything runs like a well-oiled machine.
But wait, there’s more. ISO 9001 isn’t just about quality control. It’s about:
Customer Confidence: Your clients will appreciate the fact that you have a certified quality management system. It gives them peace of mind, knowing that you’re committed to delivering top-notch products and services.
Improved Efficiency: By standardizing processes, you minimize errors, cut waste, and optimize resources. Who doesn’t want that?
Better Decision-Making: With ISO 9001, you collect data on your processes, which translates into informed decisions. You won’t be flying blind anymore.
How ISO 9001 Certification Works: The Step-by-Step Process
Let’s be real—getting ISO 9001 certified is a process. But it’s not as overwhelming as it seems. Think of it like preparing for a big test. You break it down, take it step-by-step, and before you know it, you’re all set. Here’s a simplified breakdown of what you’ll need to do:
1. Understand the Standard
Before you do anything, familiarize yourself with what ISO 9001 actually involves. It’s not just about ticking boxes on a form; it’s about embedding a culture of quality management across your company. The standard touches on leadership, planning, support, operation, performance evaluation, and improvement.
2. Assess Your Current Processes
Take a long, hard look at your current systems. Are they efficient? Do they minimize errors? Identify gaps that could use improvement. This assessment is vital for figuring out where your current system stands in comparison to ISO 9001 requirements.
3. Train Your Team
No one can do it alone. You’ll need to get your team on board and ensure everyone understands their role in the process. Training isn’t just for the higher-ups; from the assembly line to the management team, everyone should know what’s expected of them.
4. Implement the Changes
Once your team is on the same page, it’s time to put the new quality management processes into action. This can include everything from revamping workflows to documenting procedures and improving internal communication.
5. Internal Audits
This step is about checking your progress. Internal audits help you identify areas where you might not be fully compliant yet. Think of it as doing a practice run before the big exam.
6. Get Certified
This is where you bring in an external ISO auditor. They’ll review everything you’ve done to ensure it meets the ISO 9001 requirements. If all goes well, you’ll get the coveted certification.
7. Maintain and Improve
ISO 9001 is not a one-and-done thing. It’s all about continuous improvement. So, even after you’re certified, you’ll need to regularly monitor processes, gather feedback, and refine your quality management system.
The Hidden Benefits: What You Didn’t Know You Needed
Okay, so we’ve talked a lot about how ISO 9001 improves efficiency, boosts customer satisfaction, and minimizes risk. But here’s something you might not have considered: it can also improve employee morale and engagement. Think about it—when your team knows that systems are in place to help them succeed and that they’re working towards a common goal, they’re more likely to feel motivated and valued.
In fact, a well-implemented quality management system fosters a sense of ownership among your employees. They don’t just show up and do their jobs—they actively contribute to creating a culture of excellence. And that’s something that pays off big time.
Overcoming Common Myths About ISO 9001
Look, we get it—change is tough. And when you hear about ISO 9001 certification, it can sound like a huge undertaking. But let’s bust a few myths that might be holding you back:
1: ISO 9001 is Only for Large Companies
Not true. ISO 9001 can benefit businesses of any size, from small workshops to massive industrial plants. It’s scalable, meaning it can be tailored to fit your specific needs.
2: ISO 9001 is Too Expensive
Sure, there’s an investment involved. But consider this: the efficiency, customer satisfaction, and brand credibility you gain often outweigh the initial costs. Plus, the long-term savings from reducing waste and defects are hard to ignore.
3: ISO 9001 Takes Too Long
While the process does take time and effort, it doesn’t have to drag on forever. With proper planning and dedication, you can be certified in a reasonable timeframe—often within 6 to 12 months, depending on the size of your business.
Final Thoughts: Should Your Company Get ISO 9001 Certified?
Here’s the thing—ISO 9001 certification is an investment in the future of your company. It’s not just about ensuring the quality of your products today; it’s about creating systems that improve and adapt with you as your company grows. It’s about setting a standard that says, “We care about quality, we care about our customers, and we’re always striving to do better.”
Sure, the road to certification can be challenging, but the payoff? It’s worth it. By embracing ISO 9001, you’re setting your company up for long-term success, building trust with customers, and improving efficiency across the board. Why wouldn’t you want that?
So, if you’re on the fence, think about this: isn’t it time your company had a system that supports quality at every level? The journey to ISO 9001 might just be the step you need to take your manufacturing or industrial business to the next level. Ready to make the move?
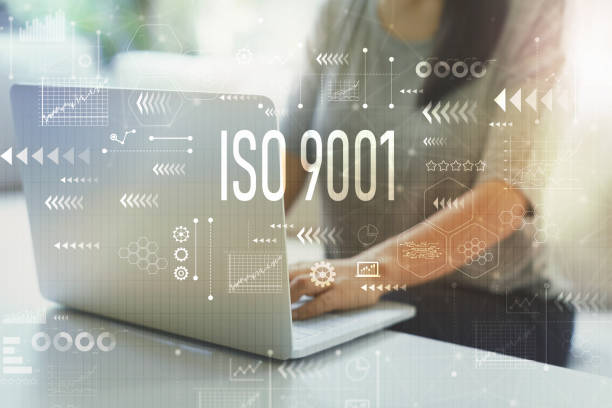