Fasteners are essential for practically all industrial applications, construction projects, and mechanical setups. The strength of these connectors, which hold components and materials together, directly impacts the longevity, functionality, and safety of machines and structures.
Despite their apparent simplicity, fasteners can malfunction in various ways, resulting in costly downtime, safety hazards, and structural damage. Whether you’re an engineer, maintenance worker, buyer, or supplier, you need to know why fasteners break and how to prevent them.
In this article, we’ll examine common fastener failures, investigate their causes, and share practical tips for keeping them working safely and effectively.
Why Fasteners Fail?
Bolts, nuts, screws, washers, and rivets are made to handle physical loads, shaking, temperature changes, and harsh environments. But they can still fail because of material problems, wrong installation, or poor design choices.
You might see:
- Structures or equipment malfunctioning
- Work halting and costly repairs
- Risks to personnel and machinery
- Increased expenses for upkeep and replacement
Because manufacturers and suppliers of industrial fasteners supply goods to vital sectors like automobiles, construction, energy, and machinery, avoiding failures is essential to fulfilling industry standards and satisfying clients.
Common Types of Fastener Failures
Fasteners can break in a number of typical ways. Let’s examine each kind so you can identify issues early and address them effectively.
Mechanical Overload
A fastener bends or breaks when it is subjected to more force than it can withstand. This occurs when:
- You use insufficiently strong fasteners.
- You chose the incorrect fastener size for the task.
- You overtighten it.
- Unexpectedly large loads are applied to the fastener.
What you will observe:
- The fastener becomes distorted by stretching or bending.
- It snaps all of a sudden.
- The attachment loosens.
Fatigue Failure
Even though no single stress seems excessive, this occurs gradually over time as the fastener is repeatedly stressed.
Why does it occur?
- Continuous tremor or moving components
- Design flaws in the fastener
- Subpar materials
- Insufficient initial tightening
What you’ll observe:
- tiny fissures that enlarge
- Slowly, the fastener becomes weaker.
- abrupt failure after a prolonged period of good operation
Corrosion-Induced Failure
Basically, your fastener is being eroded by rust and chemical damage.
Typical reasons:
- exposure to chemicals, salt, or water
- Using environmentally harmful metals
- A reaction is produced when two distinct metals come into contact.
- Absence of protective coatings
Findings:
- Rust and pitting on the exterior
- The fastener becomes weaker and thinner.
- It gets stuck or is difficult to get rid of.
Thread Stripping
This occurs when the bolt or nut spiral grooves sustain damage.
Why does it occurs?
- Excessive tightening
- At an angle, inserting the fastener
- Incompatible thread types
- Threads that are worn out
Issues you’ll encounter:
- The connection breaks.
- The joint may totally fail.
- You will require costly repairs.
Hydrogen Embrittlement
When hydrogen enters high-strength steel fasteners, it causes brittleness, which is a cunning issue.
Reasons:
- Specific plating procedures
- Using extremely powerful fasteners without the necessary care
- exposure to corrosive environments or moisture
What takes place:
- The fastener abruptly and unexpectedly breaks.
- It is difficult to identify before it fails.
- It may result in major safety issues.
Root Causes Behind Fastener Failures
Finding out why fasteners fail helps manufacturers and suppliers provide better solutions and stop problems from happening again.
Material Selection and Quality
The durability and functionality of a fastener are significantly impacted by the material you select.
Inadequate alloys or steel frequently don’t have the necessary strength or resistance to rust.
Inadequate heat treatment may result in uneven hardness or internal stress.
Inadequate testing could result in inconsistent fastener batches.
The top Indian manufacturers use high-quality materials, adhere to international standards like ASTM, ISO, and DIN, and concentrate on meticulous quality checks.
Improper Design and Specification
When selecting the appropriate fasteners for the task, the load, size, grade, and environment must all be taken into account.
- Things won’t clamp correctly if the bolts are too small or the thread types are incorrect.
- Early failures result from ignoring the effects of movement and repeated stress on fasteners.
- Ignoring environmental factors leads to brittleness or rust.
Manufacturers frequently collaborate with customers to develop unique designs or assist in selecting appropriate standard products.
Inadequate Installation Practices
Even top-quality fasteners will fail if not installed correctly.
Tightening too much damages threads and stretches the fastener.
- Not tightening enough leads to loosening and vibration problems.
- Using the wrong tools results in uneven pressure.
- Dirt, oil, or rust on threads reduces friction and messes up torque values.
Suppliers usually provide guidelines on how to install fasteners properly.
Environmental Exposure
Fastener breakdown is accelerated by chemicals, corrosive environments, and high temperatures.
- Problems with rust and metal interaction arise in coastal areas.
- Special rust-resistant fasteners are required in chemical plants.
- Changes in temperature cause expansion and contraction, which results in loosening.
- Using resistant materials (like stainless steel) and suitable coatings (like galvanisation or zinc plating) can protect against environmental damage.
Preventive Measures to Avoid Fastener Failures
Preventing failures means using quality materials, good design, and proper installation.
Choosing the Right Fastener Manufacturer
The first step in choosing trustworthy fasteners is to choose manufacturers who:
- Use high-quality raw materials and perform a thorough quality check. Observe global norms
- Provide a range of goods, such as specialty fasteners.
- Offer customisation and technical support.
India is home to some of the world’s top manufacturers, which provide high-quality fasteners for various industries at competitive prices.
Material and Coating Selection
Prevent rust and make fasteners last longer by choosing:
- Stainless steel (types 304, 316) for high rust resistance
- Galvanised or zinc coatings for moderate protection
- Hot-dip galvanising for heavy outdoor use
- Special coatings like PTFE for chemical resistance
- Talk to suppliers to find the best materials for your specific conditions.
Correct Specification and Engineering
Engage suppliers and engineers as soon as possible to:
- Select the right sizes and grades for your loads.
- Consider the effects of repeated stress on fasteners.
- Incorporate environmental considerations and safety margins.
- For dependability, use products that adhere to standards.
- Overload and fatigue risks are decreased by good engineering.
Installation Best Practices
A lot of failures begin during installation. For achievement:
- Make use of torque wrenches that have been calibrated and adhere to the suggested tightening values.
- Don’t tighten too much or too little.
- Use lubricants only as advised.
- Teach installers how to do things correctly.
- Check joints frequently for rust or loosening.
By taking these actions, thread damage, loosening, and fatigue failure are decreased.
Regular Inspection and Maintenance
Regular inspections are necessary for even the best fasteners:
- Check for deformation, cracks, or rust.
- Retighten important fasteners in accordance with timetables.
- Replace any damaged or worn fasteners.
- Employ testing methods to identify cracks early. Proper maintenance helps identify issues before they result in costly malfunctions.
Avoiding Hydrogen Embrittlement
Manufacturers avoid issues with hydrogen by:
- Making use of appropriate heat treatments and plating procedures
- Choosing materials that are less susceptible to hydrogen
- Observing stringent quality controls
Verify that your suppliers adhere to these guidelines, particularly when it comes to essential high-strength fasteners.
How to Choose a Fastener Manufacturer for Quality Fasteners
If you want strong, dependable fasteners for your projects, choosing the right manufacturer is crucial. Poor fasteners can be hazardous, break too easily, and increase the cost of repairs or lost productivity. Before choosing a manufacturer, you should take your time and carefully evaluate them to avoid these problems.
The following easy steps will help you find a quality fastener manufacturer:
1. Asset manufacturer’s industry experience and Reputation.
Experience and a solid reputation are typically indicators of a manufacturer’s ability to consistently produce high-quality products.
- Years in Business: A seasoned manufacturer usually has reputable suppliers, tried-and-true techniques, and in-depth awareness of the many fastener uses.
- Consumers and sectors: Ask if the manufacturer has experience in heavy machinery, cars, buildings, or aeroplanes.
- Remarks and references: Ask pleased customers for testimonials, suggestions, or contact information that promotes exceptional products and services.
- Certificates & Awards: Acknowledgments such as ISO 9001 (quality control) or particular industry certifications increase confidence and reflect a commitment to upholding quality standards.
2. Evaluate Material Sourcing and Quality Control Procedures
Great fasteners are constructed on a foundation of great materials and meticulous quality tests.
- Raw Material Source: Reputable companies get their materials from trustworthy vendors who know the specific grade and composition needed for your usage.
- Material Traceability: Being able to trace materials back to their origins is important for accountability and ensuring consistent quality, not just for paperwork.
- Check to see if they conduct in-house testing on both the raw materials and the final fasteners, including strength testing, hardness checks, and chemical analyses.
- Procedures for Quality Control: Look for indications that they take quality seriously, such as visual examinations of each component, measurements of dimensions, thread checks, and batch testing to identify issues.
3. Confirm Compliance with Industry Standards and Specifications
Let’s face it: if you want fasteners to be safe and functional, they must meet certain standards.
- Criteria for adherence: Confirm that you fulfil the requirements of your industry and location, such as ASTM, ISO, DIN, JIS, or ASME.
- Availability of Certification: Request supplemental materials, such as relevant test findings, certifications of inspection, explanations of compliance, and more.
- Adaptability: If you need something unusual, please contact us so that we may produce coatings, notes, or sizes that match your exact requirements.
4. Review Manufacturing Technology and Capabilities
The approaches and equipment utilized have a considerable impact on the quality of the permanent pieces.
- Automation and Machines: Two current examples of visually beautiful gadgets are CNC machines and thread rollers. It also gives enhanced precision and dependability.
- Knowledge about Heat Treatment: Proper heat treatment is vital for durability and strength. Be sure to get to know one another and adhere to tight protocols.
- Surface Treatment and Coating: Serious manufacturers should offer a choice of coatings, such as zinc coatings and distortions, to avoid rust and meet the standards.
- Production Capacity: Can I manage my order amount without rushing or cutting corners? You need to be aware of this from the start.
5. Inspect Product Range and Availability
It simply facilitates lifespan to have a reliable source for all fixed elements.
- Wide range of products: Make sure you have all the traditional fixed elements you need, including bolts and nuts and all unique fixed elements related to the industry.
- Stock Management: Adopting the right stocking practices will allow you to pick up your goods rapidly and avoid a backlog if necessary.
- OEM and mass supply experience: OEMs or manufacturers who often deal with large orders can support ongoing projects and create long-term cooperation.
Conclusion
By choosing the reliable fastener manufacturer, you can receive high-quality products and excellent after-sales support.
Investing in high-quality materials, selecting the correct elements, and using them carefully during installation will help prevent errors and ensure the structure’s safety for many years.
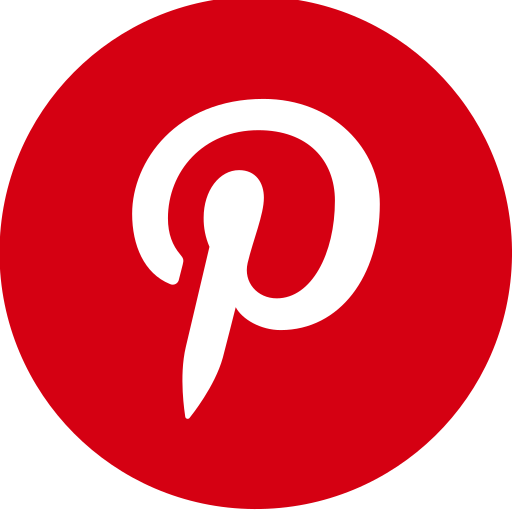