Introduction: The Rise of Predictive Maintenance in Manufacturing
As the manufacturing industry competes and time being is very important, operational efficiency and low downtime are essential nowadays. Predictive Maintenance: PdM is not reactive or preventive, Predictive Maintenance (PdM) is disrupting the way reliability thinks and works. PdM is real-time equipment monitoring that uses data analytics machine learning, sensors to predict failure & schedule maintenance ahead of time. It optimizes assets, lowers costs and improves productivity by following this preventive methodology. These new advancements are being adopted quickly with the increase of Industry 4.0 and IIoT that are paving the way for PdM in various manufacturing verticals.
How Predictive Maintenance Software Works?
- Data Acquisition: Connecting to sensors (vibration, temperature, pressure, acoustic, ultrasonic, oil analysis etc.) existing industrial control systems (PLCs and SCADAs etc.) as well as performing a real-time stream, historical data about performance of equipment’s as well environmental information’s. A temperature sensor on a motor may send continuous temperature readings to the software for example.
- Storing and Organizing Data: Many assets will capture large volumes of data, which need to be stored and organized in a structured manner whether that pile up in on-premises or preferably also with cloud-based database.
- Data Analytics: Various analytical approaches from statistical analysis, machine learning algorithms (like regression, classification and time-series analysis) as well as artificial intelligence used to detect trends or anomalies and correlations within the data that may signify equipment degradation/causes for the failure. For example, machine learning algorithms can be trained to identify the normal vibration signature of a pump and raise an alarm on any future deviation indicating approaching bearing failure.
- Prediction and Diagnosis of Faults: Analyzing the data for fault predictions as well as diagnosis in some cases of when an operational piece of equipment may fail. Perhaps the software will tell you that a certain CNC machine spindle has a 70% probability of failing within the next month as vibration levels are going up.
- Alerts/Notifications: Issue alerts and notifications when suspected issues are noted, or date to failure is getting close allowing maintenance to take preemptive action. Alerts can be delivered by email, SMS or connected to other maintenance management systems.
- Reporting & Visualizations: Establish dashboards and reports that capture overall health of equipment, performance trends from sensor data, planned maintenance scheduling, PdM driven immediate impact to uptime/cost performance metrics etc. Maintenance managers can use these dashboards to return the big plant view of asset health.
- CMMS/EAM Systems Integration: Generally integrating with Computerized Maintenance Management Systems (CMMS), or Enterprise Asset Management (EAM) solutions to create work orders, schedule maintenance and track the maintenance history automatically.
When evaluating PdM software, consider the following factors:
Ease of Use & Implementation:
- Reducing the learning curve for maintenance teams keeps the user interface (UI) simple so that it will be adopted quickly and used properly as well.
- A process with clean implementation the documentation is clear, and vendor support exists will reduce operability disruption and increase time-to-value.
- Think about how difficult it will be to integrate into existing systems, a seamless integration generally means very little data crossing and compatibility problems.
Analytics Capabilities:
- Machine learning algorithms (regression, classification) are paramount to providing the required accuracy in fault prediction and diagnostics with some other strong analytical techniques
- By adapting predictive models to your equipment failure modes and operating conditions, you can fine-tune the software with customizable predictive models.
- Examine if the software is resistant to time series data ingestion and if the software can perform failure mode and effect analysis.
Scalability:
- As your plant grows, the software must scale with the expanding number of assets and data volume for long-term usability.
- Cloud solutions are generally more scalable in terms of cloud storage and computing than the on-premises systems with easy provisioning of storage as well computing resources will go.
- Make sure the system can accommodate future sensor installments and higher frequency data collection.
Reporting & Visualization:
- Instant real time dashboards for equipment health and performance trend insights to help make data-informed decisions
- Reports on the KPIs associated with your operations enable you to understand how you are doing with your PdM program.
- If the software allows you to build custom reports and also export data into additional business intelligence tools.
Alerting & Notification:
- Timely and actionable alerts, that are sent as email/SMS/mobile push notifications to carry out maintenance quick That Include tailoring alerts to exact equipment conditions and severity levels through notification rules which will help to eliminate alarm fatigue.
- The alert system needs to have faulty information (of course) and machine identification.
Mobile Accessibility:
- Mobile accessibility to plant floor keeps maintenance techs from accessing live critical data and performing tasks making them more efficient to address issues with promptness.
- Basic features like work order management, data visualization and alerts notification that mobile apps should have. Try out the usability of the apps and response time of the same across various mobile operating systems.
Cost & ROI:
- A holistic total cost of ownership, including software licenses, implementation and maintenance costs is needed for budgeting.
- Determine how the software will return to invest (ROI) by lowering downtime, saving money, and increasing efficiency.
- Keep in mind, long term cost of the software (updates and maintenance), as well as support packages available
Key Benefits: Cost Savings, Efficiency, and Longevity
- Cost Savings: PdM is providing close to zero-loss downtime by way of predicted failure, thus not requiring production to temporarily halt for preventive mechanical repairs. The optimized maintenance schedules reduce labor & material cost, the accurate spare parts forecasting avoids stockouts and overstocks. In addition, finding and fixing opportunities for inefficiencies will lower your utility bills.
- Efficiency: PdM improves efficiency as OEE, and up time are maximized with predictive maintenance. Consistent schedules, better plans, faster problem resolution for assets making them better & of higher quality. It increases the productivity of your team by giving data support and heavy focused maintenance.
- Lifespan: PdM helps prolong the operational life of equipment by identifying and correcting early signs of wear, so expensive replacements are not necessary. Continued proactive maintenance for the asset increases its reliability that in turn reduces the possibility of unplanned failure. By gathering this data, the asset health and failure modes can be learnt, and long-term asset management decisions are made with such insights.
Conclusion:
PdM in manufacturing is the future, and technology will create that promise. As the use of AI and ML will result in better estimations, predictions as well wider IoT/sensor technologies can provide holistic data collection in this regard. Edge computing for immediate analysis, digital twin for better predictive models using simulations will make all this happen. AR/VR: Improve the maintenance process PdM will be fundamental when it comes to sustainability. PdMaaS will make these technologies accessible for everyone and the basics will apply throughout the supply chain.
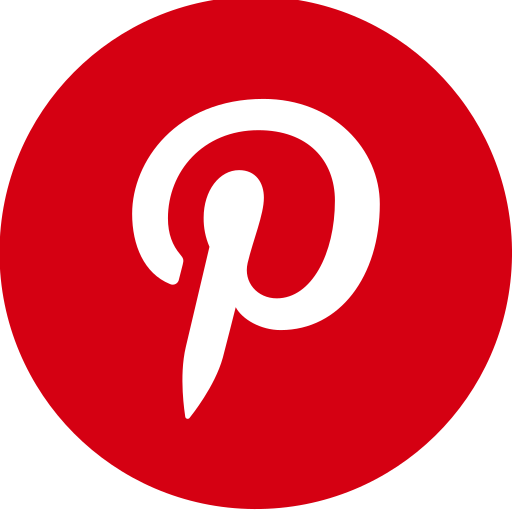